Having a clear overview of your stock is essential for effective inventory management. The Stock Overview feature in our ERP system provides a comprehensive snapshot of your products, categories, and quantities across various storage locations. With this feature, you can quickly assess your stock levels, track product movements, and make informed decisions to optimize your supply chain operations.
By organizing your inventory details into easily accessible fields, the Stock Overview feature ensures that you always have real-time insights into your stock status, helping you prevent stockouts, avoid overstocking, and streamline warehouse operations.
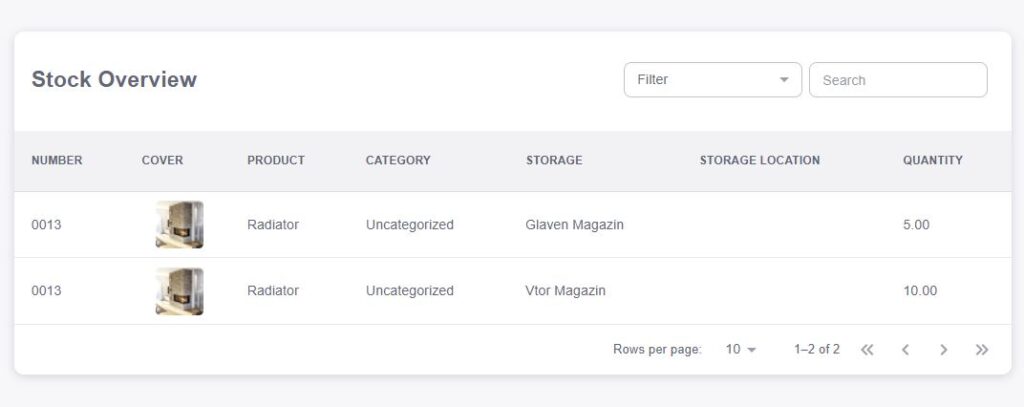
Number
The Number field provides a unique identifier for each stock entry. This could be a reference number for tracking specific items, orders, or batches. The unique number helps quickly pinpoint specific inventory entries, making stock management more efficient.Cover
The Cover field often refers to a specific batch, SKU, or variant of a product. It helps categorize or distinguish different versions or packaging of the same product. This feature is particularly useful when managing multiple variations of a product (e.g., different sizes, colors, or models).Product
The Product field lists the name of the individual items or goods in your inventory. By tracking each product, you can gain insights into what’s in stock, its usage rate, and other critical data. Having clear product information allows you to monitor trends, reorder stock in a timely manner, and ensure inventory levels match demand.Category
The Category field groups your products into logical classifications. Categorizing products based on type, function, or other relevant criteria helps organize your inventory and makes it easier to find and manage items. For example, you could categorize products as “Electronics,” “Clothing,” or “Perishable Goods” to streamline tracking and reporting.Storage
The Storage field identifies the specific warehouse or storage area where the product is kept. With multiple storage locations, this field helps you track where your stock is physically located, ensuring easy access and improved stock management. Whether it’s a specific warehouse, section, or shelf, knowing the storage area reduces time spent searching for items.Storage Location
The Storage Location field provides even more specific details about where a product is stored within the storage area. This might include a specific aisle, shelf, or bin. By being able to track exactly where an item is located, you can optimize your warehouse layout, improve stock retrieval times, and prevent misplacement of products.Quantity
The Quantity field shows the current stock level for each product in a specific storage location. It allows you to track the number of units available, so you can quickly assess whether you have enough stock to fulfill orders or if replenishment is needed. This field helps ensure that inventory levels remain balanced, preventing stockouts or excess stock that could lead to wasted space.